Features
- Fully featured PLD system optimized for the use in a synchrotron beamline
- Compact design and integrated tranfer mechanism allow installation on goniometer within minutes
- Precision sample manipulator enables high-resolution substrate rotation and tilt for diffraction studies
- Laser heating for substrate temperatures up to 1200°C
- Target manipulator for eight targets, narrow design for wide angular accessibility of substrate
- Variable target-substrate distance: 35 mm to 100 mm
- Split deposition chamber design, easy access to all components for maintenance and alignment
- Beryllium X-ray windows cover 55° in the horizontal plane (for 2θ = 110°) and 70° in the vertical plane (for 2θ = 70° in a grazing incidence geometry)
- Integrated load-lock chamber with sample storage
- Differentially pumped RHEED system (for chamber pressures up to 0.1 mbar) with motorized gun adjustment
- YAG laser for PLD at various wavelengths (UV, visible, IR)
- Gas supply for two different process gases, PID pressure control via flow controllers and motorized leak valve
Introduction
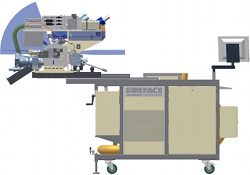
Transfer mechanism
Click to enlarge
Precise knowledge of the mechanisms that influence interface formation and growth of thin films is a key to the development of functional thin film materials. X-ray diffraction and reflection employing synchrotron radiation is one important method to study structure and interfaces of thin films. It is vital, however, that such samples are not exposed to atmosphere, since even a submonolayer of contamination could disrupt surface effects or alter thin films.
The SURFACE In-Situ Beamline PLD System is a fully featured pulsed laser deposition system optimized for the use in a synchrotron beamline. The compact footprint of the design enables the installation of the system on a goniometer.
The system maintains the versatility of a standard laboratory system, like a target carousel for multiple targets, a high-pressure RHEED system, a laser-heating system for sample temperatures up to 1200°C, and a load-lock system with vacuum sample storage. A sample manipulator with ultra-precise rotation (±135° around an axis perpendicular to the sample surface), translation (±6 mm in x/y, 3 mm in z direction), and tilt (±5°) motions enables diffraction studies in different geometries. The angular resolution of the manipulator is better than 0.001°. The compact setup leaves enough room for detector movement on horizontal and vertical circles around the system, with a beam exit window covering 55° in the horizontal plane (for 2θ = 110°) and 70° in the vertical plane (for 2θ = 70° in a grazing incidence geometry).
All relevant system functions are automated and remote controllable, thus system access is not necessary during an experiment.
System Transfer
The whole PLD system can be moved on and off the goniometer within minutes. A transfer and lifting mechanism is built into the control rack. Guide pins ensure that the system is precisely positioned on the goniometer so that realignment of the system position is not necessary. When not placed on the goniometer, the PLD system rests on its control rack and remains fully functional. In this way PLD growth processes can be optimized ex-situ, and the synchrotron facility is only occupied during the actual in-situ analysis.
Sample Manipulator
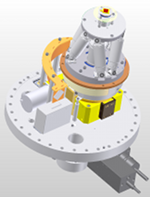
Sample manipulator
Click to enlarge
The sample manipulator holds 10×10 mm2 substrates. A hexapod facilitates alignment of the sample relative to the incident X-rays. The sample can be tilted by ±5° with 0.001° resolution around the x and y axes (the x and y axes lie in the surface plane of the sample). It can be shifted in z direction (perpendicular to the sample surface) by 3 mm to compensate for different substrate thicknesses. A ±6 mm shift in x and y direction enables scans at different positions of the sample surface.
A precision rotation stage rotates the sample by ±135°, with better than 0.001° resolution. This feature can be used to perform diffraction studies in grazing incidence geometry and to align the sample for RHEED analysis.
Both hexapod and rotation stage are mounted inside the vacuum chamber to avoid deterioration of the high precision positioning caused by the extra forces of vacuum bellows or rotational feedthroughs.
The sample is heated from its backside by a laser heating system. This keeps the total heat load of the system low while enabling sample temperatures up to 1200°C. A tracking system centers the heating laser beam on the sample even while it is moved using hexapod or rotation stage.
The sample manipulator flange is rigidly mounted to the support frame of the system and holds the vacuum chamber. In this way the chamber can be opened for maintenance while the sample manipulator alignment relative to the goniometer is not changed.
Target Manipulator – Feature Flange
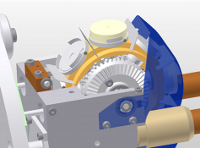
Target manipulator
Click to enlarge
The PLD target manipulator features an especially narrow design so that a wide angular range is accessible by the incident and diffracted X-ray beams even at low target-substrate distances. It holds eight targets with 1" diameter and supports target rotation and toggling motions for even target wear. All targets are separated by shields and the targets not in use are covered to avoid cross contamination. The distance between target and substrate can be varied between 35 and 100 mm. The manipulator flange can be opened and slides out on guide rails for quick target exchange.
The PLD target flange could easily be exchanged for a flange holding sources for other deposition techniques, e.g. sputtering sources or effusion cells.
Deposition Chamber
The deposition chamber is split into two halves. The first part is attached to the substrate manipulator flange and holds the vacuum pump and pressure gauges. The second part holds the beryllium windows, laser window, viewports, RHEED, etc. This part can be detached and sled outwards to enable access to the substrate manipulator, without changing the substrate manipulator alignment relative to the system frame and goniometer. This is especially useful for initial system alignment purposes, as now optical means for substrate position alignment can be employed and full access to the substrate is possible.
The beryllium windows sit in special steel frames and are o-ring sealed. This facilitates assembly and maintenance compared to welded beryllium windows. Shutters are mounted at the inside of the window frames and can be closed during PLD deposition to minimize coating of the beryllium while no synchrotron measurement is performed.
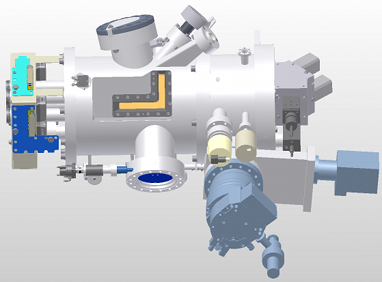
Split design of deposition chamber
Click to enlarge
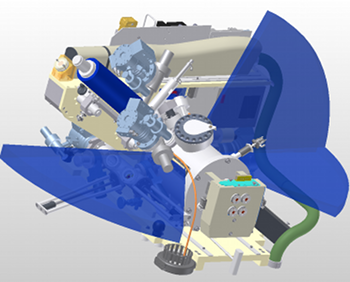
Angular ranges of Be windows
Click to enlarge
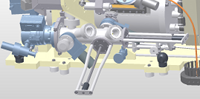
Load Lock
Click to enlarge
Load Lock
A load lock chamber is integrated into the system. It enables sample loading without breaking the main chamber vacuum and also serves as vacuum storage for up to 6 samples. The load lock is coupled to the main chamber with a quick flange connection. It is mounted to hinges, so that it can move away from the main chamber once the quick flange connection is opened. In this way the main chamber can be opened for maintenance or target exchange while the load lock remains evacuated.
RHEED
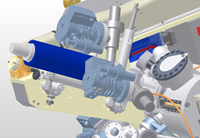
RHEED
Click to enlarge
A differentially pumped RHEED (reflective high energy electron diffraction) system is attached to the main chamber of the system. Its two pumping stages enable RHEED analysis of the deposited thin films at chamber pressures up to 0.1 mbar. The electron gun is attached to a manipulator that allows precise positioning of the electron beam on the sample and alignment of the incidence angle between 0° and 3° relative to the sample surface.
All functions of the RHEED including the mechanical gun positioning are automated and remote controlled, so RHEED analysis and synchrotron diffraction can be performed simultaneously.
YAG Laser and Laser Optics
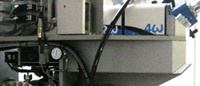
Laser beam line
Click to enlarge
A YAG laser is used for the PLD process. It enables thin film deposition as various wavelengths (UV–visible–IR). Its compact envelope enables integration onto the chamber support frame, so that the whole laser system is moved with the chamber by the goniometer.
The laser beam is guided towards the PLD target by several mirrors and the focusing lens. The lens position is variable and is changed via a motor. Thus the laser spot size can be adjusted and also held constant at various target-substrate distances. A motorized deflection mirror automatically aims the laser at the target and compensates for the different target positions.
Process Gas Supply
Two process gases can be admitted to the deposition chamber. The gas flow is controlled via flow controllers and a motorized leak valve. In this way, the whole process pressure range from 10−5 mbar to 0.5 mbar is covered. The selected process pressure is held constant by a built-in PID control loop.